Insulating your basement ceiling is essential for maintaining energy efficiency, improving comfort, and adhering to building regulations. However, it’s crucial to be aware of the basement ceiling insulation code requirements to ensure that your home stays compliant with local building standards. These codes are in place to ensure the safety, performance, and energy efficiency of your home’s insulation system, especially in colder climates where heat loss can be a significant issue.
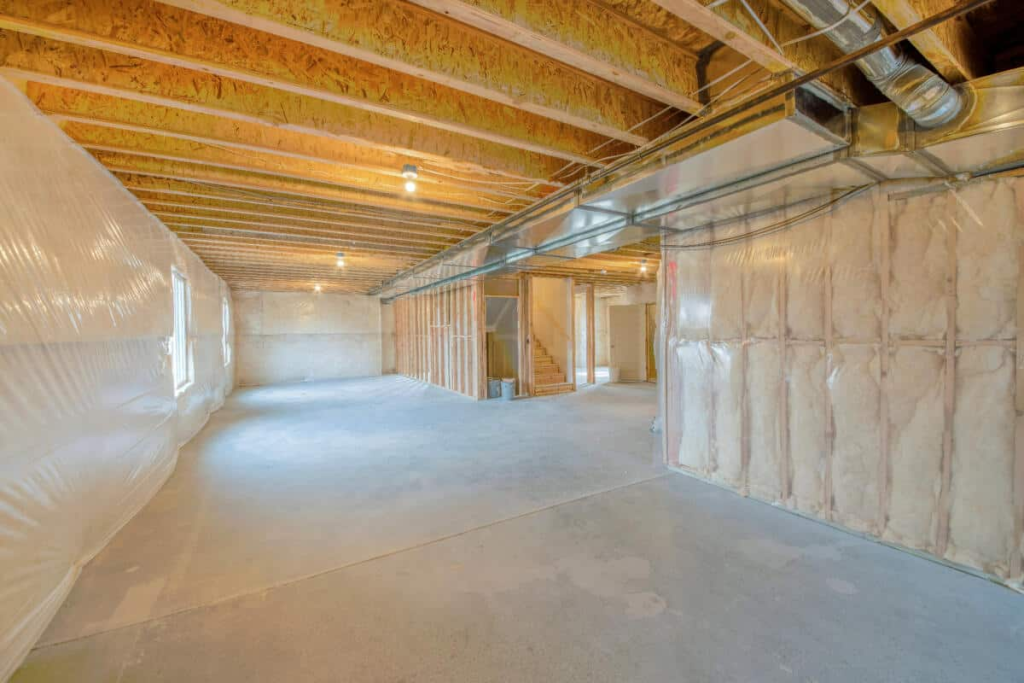
In this article, we’ll provide a comprehensive guide to the basement ceiling insulation code, including its importance, relevant standards, and factors to consider when insulating your basement ceiling. Whether you’re a homeowner, contractor, or DIY enthusiast, understanding these codes is critical for achieving the best results in terms of comfort, energy savings, and safety.
Why Basement Ceiling Insulation Matters
Before diving into specific code requirements, it’s important to understand why basement ceiling insulation is essential. Basements often suffer from poor insulation, leading to several issues:
- Heat Loss: Without adequate insulation, basements can become cold during winter, causing the rooms above them to lose heat. This increases energy consumption as heating systems have to work harder.
- Moisture Control: Insulation also helps in controlling moisture, which is crucial in basements that are prone to dampness and condensation. Proper insulation prevents mold growth and protects the structural integrity of your home.
- Soundproofing: Insulating the basement ceiling can reduce noise transfer between floors, making the home more comfortable, particularly in houses with entertainment or utility rooms in the basement.
- Energy Efficiency: Proper insulation ensures energy efficiency, lowering heating and cooling costs throughout the year.
Given these benefits, many building codes outline strict insulation requirements to help homeowners protect their investment and ensure a safe living environment.
Understanding Basement Ceiling Insulation Code
The basement ceiling insulation code is a set of standards and regulations provided by local building authorities, as well as national codes like the International Residential Code (IRC) and the International Energy Conservation Code (IECC). These codes establish the minimum R-value (thermal resistance) needed for different parts of a home, including basements.
What Is an R-Value?
The R-value of insulation refers to its ability to resist heat flow. The higher the R-value, the better the insulation’s performance. Different areas of the home, such as walls, attics, and basements, have specific R-value requirements based on the local climate zone.
For basements, the R-value for ceiling insulation can vary, but it typically ranges between R-19 and R-30. This ensures that the basement stays insulated against temperature fluctuations, especially in colder regions.
The Basement Ceiling Insulation Code Requirements
In many regions, basement insulation requirements are detailed by both local and national building codes. Here’s a breakdown of what you need to know about basement ceiling insulation code standards:
1. International Residential Code (IRC)
The IRC is one of the most widely used building codes in the United States and provides guidance on insulation for various parts of a home, including basements. According to IRC, basement ceilings that are adjacent to conditioned spaces should have insulation that meets the minimum R-value specified for the climate zone.
- Climate Zone 1-2: R-13 to R-15
- Climate Zone 3-4: R-19
- Climate Zone 5-8: R-30
These climate zones represent different geographical regions, where higher numbers indicate colder climates that require better insulation.
2. International Energy Conservation Code (IECC)
The IECC also sets insulation standards for energy efficiency, helping to reduce energy consumption in homes. Like the IRC, the IECC’s insulation requirements are broken down by climate zone. The specific R-value requirements for basement ceilings depend on whether the space above the basement is conditioned or unconditioned.
For instance:
- If the basement is unconditioned and the ceiling separates it from a conditioned living space, the R-value needs to comply with the standard requirements for floor insulation based on the climate zone.
- For conditioned basements, the walls should meet the code-specified R-value.
3. Local Building Codes
In addition to national codes, local municipalities may have their own specific insulation requirements. It is important to check with your local building authority before beginning any insulation project to ensure compliance with any additional regulations.
Some local codes may also specify whether a vapor barrier is required in basement insulation to prevent moisture issues. This can be particularly important in areas with high humidity or prone to water leaks.
4. Fire Safety Codes
In many regions, fire safety regulations play a role in how insulation is installed in basements. For example, building codes may require certain types of insulation, such as those with fire-resistant properties, or the installation of fire-blocking materials in specific areas.
Insulation in basement ceilings should comply with fire safety codes, especially if there are electrical wires or pipes running through the ceiling. Fiberglass and mineral wool are often recommended for their fire-retardant qualities.
Factors to Consider When Insulating a Basement Ceiling
To successfully meet the basement ceiling insulation code and achieve the best results, several key factors must be considered during the insulation process. These factors will help determine the right type of insulation and installation techniques for your home.
1. Climate Zone
As mentioned, your local climate zone will heavily influence the required R-value for basement ceiling insulation. Homes in colder climates will need insulation with a higher R-value to ensure the basement remains warm during winter months, while homes in warmer areas can use lower R-value insulation.
2. Unconditioned vs. Conditioned Basements
The type of basement you’re insulating also impacts your choice of insulation and how much you need. In an unconditioned basement (where the basement itself is not heated or cooled), it’s crucial to insulate the ceiling to maintain the energy efficiency of the home. For conditioned basements, the walls might require insulation more than the ceiling, depending on local codes.
3. Moisture Control
Since basements are prone to moisture issues, especially in regions with high humidity or heavy rainfall, moisture control is vital during insulation. If moisture builds up in the insulation, it can lead to mold growth, structural damage, and reduced insulation effectiveness.
Installing a vapor barrier can help prevent moisture from penetrating the insulation. This is especially important if you’re using materials like fiberglass, which can absorb water and lose effectiveness.
4. Soundproofing
In addition to thermal insulation, basement ceiling insulation can also be used to reduce noise transmission between floors. Insulation materials like cellulose or mineral wool can offer soundproofing benefits, making them a good choice if you’re using the basement as a living area, home office, or entertainment space.
5. Cost and Materials
The type of insulation material you choose will affect the cost and performance of the insulation. Common insulation materials for basement ceilings include:
- Fiberglass Batts: A cost-effective option with good thermal performance. Fiberglass is easy to install and widely used in basement insulation projects.
- Spray Foam Insulation: This option provides excellent thermal resistance and acts as both insulation and a vapor barrier. However, it can be more expensive than other materials.
- Mineral Wool: This material offers both thermal and soundproofing benefits, as well as fire resistance, making it an excellent choice for basements.
Installation Tips for Meeting Basement Ceiling Insulation Code
Once you’ve selected the right insulation material and determined the required R-value based on your climate zone and local code, it’s time to install the insulation. Here are some tips to ensure your installation meets code and provides the desired benefits:
1. Seal Gaps and Cracks
Before installing insulation, make sure to seal any gaps, cracks, or holes in the ceiling or walls. This will prevent air leakage and moisture infiltration, ensuring your insulation performs at its best.
2. Install Vapor Barriers
In basements with high humidity levels, a vapor barrier should be installed to prevent moisture from damaging the insulation. This is especially important when using materials like fiberglass, which can lose effectiveness when wet.
3. Use the Right Tools
Proper insulation installation requires specific tools, such as insulation knives, staplers, and protective gear. Make sure to follow the manufacturer’s instructions for both the insulation material and any vapor barrier.
4. Follow Local Code Guidelines
Always refer to your local building codes before starting your insulation project. Codes may differ depending on your location, and it’s essential to stay compliant with these regulations to avoid potential fines or complications during future home inspections.
Conclusion
Meeting the basement ceiling insulation code is crucial for maintaining energy efficiency, improving comfort, and protecting your home from potential moisture issues. By understanding the specific insulation requirements for your climate zone and local codes, you can make informed decisions about the type of insulation to use and how to install it properly.
When properly insulated, a basement can become a more comfortable and usable space, whether for storage, living, or entertainment. Investing in the right insulation materials and techniques will pay off in the form of lower energy bills, better soundproofing, and a more comfortable home.